青海供应称重给煤机生产厂家
发布时间:2023-05-15 00:44:03
青海供应称重给煤机生产厂家
电子皮带秤在称重操作过程中瞬间总流量在一定的范畴内变化是常规的,但假如颤动过大,那么就需要查验皮带秤仪表盘间距值设置是不是过大,称重感应器是不是毁坏,秤架是不是被石头等卡死,皮带输送机是不是跑偏等。间距校正的转变,一般与系统软件的测量构件和皮带支撑力的改变相关,关键因素有:运输飞机皮带支撑力发生了转变,应做好调节,调节办法跟上面一样。限速感应器滚桶滚动;增加限速滚桶和往返皮带中间的包边,避免滚桶跑偏而导致失转状况。

青海供应称重给煤机生产厂家
定量皮带秤又被称为定量振动给料机,关键为固态纤维状物料持续称重的计量机器设备,如小块、颗粒物、粉末状物等。定量皮带秤由顶层预振动给料机,定量皮带秤,称重感应器,验证设备、称重控制板、电气设备控制技术及声卡机架等构成。定量皮带秤连接客户自动配料系统,顶层预振动给料机与料斗相接,系统软件运作时,根据PLC控制称重控制板进到校准方式。顶层预振动给料机遇定量皮带秤与此同时关机,验证设备全自动将砝码置放于称重皮带输送机上开展静态数据标准砝码校准,选用静态数据标准砝码校准定量皮带秤后,顶层预振动给料机与定量皮带秤与此同时运行,顶层预振动给料机送料,操纵料流长短低于定量皮带秤长短,称重控制板获得动态性称重料数值;
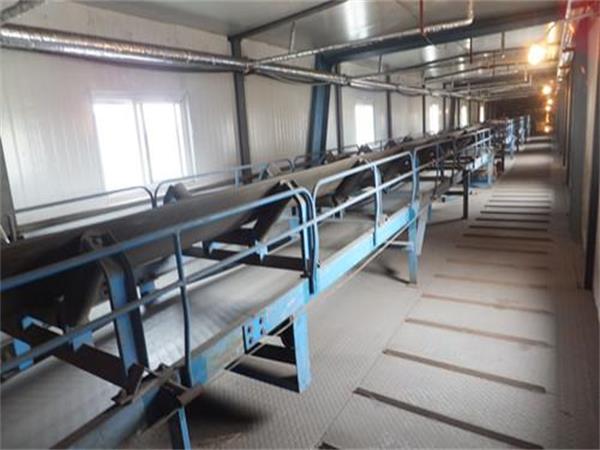
青海供应称重给煤机生产厂家
针对皮带计量秤来讲,不用终止秤重。强劲的存储空间储存作用。它非常容易储存、查看和打印出数据信息。国际性计量检定机构和中国相关部门的验证。皮带秤显示仪表并不是简易的新代数控系统,只是一种智能化系统水平高、储存工作能力强的微型机。皮带秤称重设备自今年初至今在国内区域内规模性安装应用,销售市场已做到1000台。微型机操纵,智能化系统水平高。起重吊装时不泊车,自动称重,实际操作简易,不危害运载高效率,合理避免过重和欠载。复印机还可以打印出装车時间、货品名字、净重、车辆皮号等数据信息。液晶显示屏和电脑键盘都是有背光灯,有利于晚间应用。显示屏显示屏或莹光动态显示,可表明秤重結果、总计秤重結果、信息内容、实际操作技术人员等,形象化便捷。抗干扰性强,适用多种自然环境。预留充电电池,当电子称关掉时,储存的信息依然能够保存。尽管输送机式皮带秤与整机型皮带秤都内置输送机以及驱动力,但切不可把二者混为一谈;嵌装型皮带秤与称重台式一体机皮带秤的理念也并不彻底等同于。输送机式皮带秤一般全是整机型皮带秤;但称重台式一体机皮带秤,能够是嵌装型的,还可以是整机型的,这2种类别都很普遍。具备称重台的整机型皮带秤的安装器是称重台及恰运作于其上的那一段皮带,而不是一台详细的输送机。安装器形式的差异立即跟称重传感器的容积相关,一样是整机型皮带秤,安装器为称重台或输送机挑选 称重传感器的容积的计算方法就不一样。

青海供应称重给煤机生产厂家
如何有目的性的处理皮带方向跑偏的难题呢?发觉皮带方向跑偏时,工作员要关机用心检查一下,寻找难题是怎么回事导致的。先皮带满载时方向跑偏,看一下是否由于初支撑力很大导致的,一加物料便会获得改正。次之如果是滚桶表层有粘接物料,立即清除,按时常常清理会避免这一状况产生;若是滚桶不水准导致的,应该马上校正,是生产制造导致的因素应从新生产加工滚桶。也有可能是安裝时轴线不直也会发生皮带方向跑偏的状况,安裝时留意这一点便会避免难题产生。对电子器件皮带秤的皮带开展维修,防止皮带损坏和衰老造成的跑偏,移速不均匀等难题,危害电子器件皮带秤的称重精确性。观查电子器件皮带秤套筒连接上有没有出现异常,常出現的情况是秤架和皮带输送机侧梁之 间有物料卡死,或是是缓冲托辊松脱。观查皮带上能否有粘料,如果有粘料,会造成电子器件皮带秤点转变,危害称重精确性。
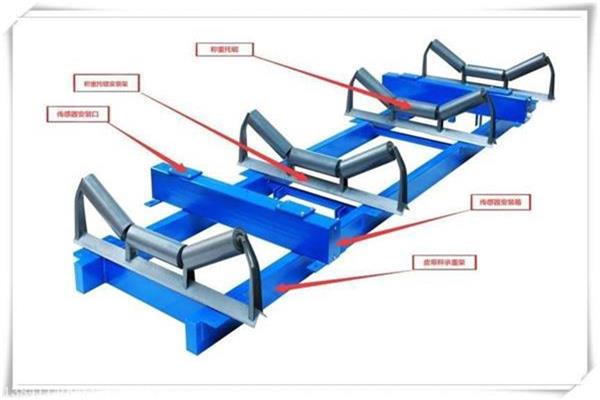
青海供应称重给煤机生产厂家
数据信号偏差包含线性降低总计控制板变大测算A/D变换偏差操纵数据信号调整偏差等。数据信号偏差的去除方式是查验系统软件各构件中间的相匹配内布线,布线应当合乎当场接线方法的要求,当发生接触点松脱电焊焊接不牢固触碰不太好有短路故障或是短路情况时,及其不按要求接地装置的状况,调料皮带秤便会造成读值偏差和称重的读值多变性。同轴电缆显示屏控制板持续搜集负荷感应器数据信号和速率数据信号,测算具体物料的总流量,并将具体总流量与流量设置开展较为。假如流量设置超过具体总流量值,则操纵变频调速器加快。假如总流量设置低于具体总流量值,则操纵頻率转化器将持续降速,并将具体走刀率与预设值开展较为,以操纵皮带速率。具体总流量值设置干总流量定量给料机的原理计量检定系统软件电子称负荷感应器数字转换器计量检定显示屏控制板关键组成计量检定自动控制系统。